A Legacy In Wood: The Art Of Cricket Bat Making
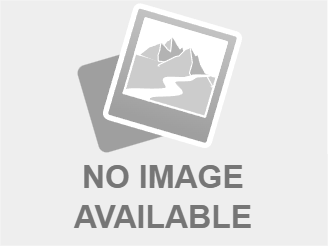
Table of Contents
The Selection of the Perfect Willow
The journey of cricket bat making begins with the selection of the raw material: the willow. English willow, renowned for its superior strength and resilience, is the undisputed king. Specifically, Grade 1 and Grade 2 English willow are favored for their exceptional close grain structure, a key characteristic influencing the bat's performance. Good willow displays a straight grain pattern with minimal blemishes, knots, or other imperfections. The selection process is rigorous and demands an experienced eye.
- Visual Inspection for Flaws: Experienced bat makers meticulously examine each piece of willow, looking for any imperfections that could compromise the bat's strength and longevity.
- Testing for Density and Strength: The density and strength of the wood are crucial. Various methods are employed to assess these factors, ensuring only the finest pieces are chosen.
- Specific Willow Growing Regions: The best willow comes from specific regions known for their climate and soil conditions, contributing to the wood's unique properties. These regions are carefully selected for optimal growth.
Shaping the Cricket Bat: From Cleaving to Carving
Once the perfect piece of willow is selected, the process of shaping the cricket bat begins. This involves cleaving the wood – splitting it along the grain to create rough bat shapes. This is followed by a series of precise cuts and shaping using specialized tools and techniques. This phase demands exceptional skill and accuracy, as the slightest error can impact the bat's balance and performance.
- Use of Specialized Tools: Axes, shaping knives, and other specialized tools are employed to carefully carve the willow into the desired profile.
- Creating the Profile: The bat's profile – its edges, shoulders, and toe – is meticulously crafted to meet specific performance requirements.
- Maintaining Symmetry and Balance: Precision is paramount; symmetry and balance are essential for optimal performance and a comfortable feel.
The Role of Hand-Crafting and Technology
Modern cricket bat making cleverly blends traditional hand-crafting techniques with advanced technologies. While many steps still rely on the skill of experienced craftspeople, technology enhances precision and efficiency. Computer Numerical Control (CNC) machines, for instance, are increasingly used for some aspects of shaping, ensuring consistent accuracy and reducing production time. However, the human touch remains vital, particularly in the finer details and finishing processes. This synergy between traditional craftsmanship and technological advancement ensures high-quality cricket bat manufacturing.
Finishing Touches: Graining, Oiling, and Branding
The final stages of cricket bat making involve several crucial finishing touches. Graining the bat's face – creating a slightly rough surface – optimizes ball contact and grip. The bat is then oiled, usually with linseed oil or tung oil, to protect the wood from moisture damage and enhance its durability. Finally, the manufacturer's logo and other markings are added, completing the branding process.
- Types of Oil Used: Linseed oil and tung oil are commonly used, each offering specific protective and performance-enhancing properties.
- The Importance of Proper Drying and Curing: Allowing the oil to properly dry and cure is essential for the bat's longevity and performance.
- Techniques for Applying Logos and Markings: Various techniques are used to apply logos and markings, ensuring they are durable and aesthetically pleasing.
Quality Control and Inspection
Stringent quality control measures are implemented throughout the cricket bat making process. Experienced inspectors meticulously check for cracks, weaknesses, or any other flaws that might compromise the bat's strength and durability. Balance, weight, and overall performance are also assessed before a bat is deemed fit for sale. This commitment to quality ensures that every cricket bat leaving the workshop meets the highest standards of performance and safety.
- Checking for Cracks or Weaknesses: Each bat undergoes thorough inspection for any signs of cracking or weakness.
- Testing for Balance and Weight: The bat's balance and weight are carefully checked to ensure they meet the player's preferences.
- Assessing Overall Quality and Performance: A final assessment is conducted to ensure the bat meets the high standards required for performance and durability.
A Legacy Forged in Wood: Preserving the Art of Cricket Bat Making
From the meticulous selection of English willow to the final quality control check, cricket bat making is a testament to craftsmanship and precision. The enduring legacy of this traditional craft lies in the skill and dedication of the artisans who continue to perfect their techniques, creating high-performance cricket bats that have stood the test of time. Discover the artistry behind your next cricket bat; invest in a handcrafted cricket bat and experience the difference. Learn more about the rich history of cricket bat making and appreciate the skill involved in creating this iconic piece of sporting equipment.
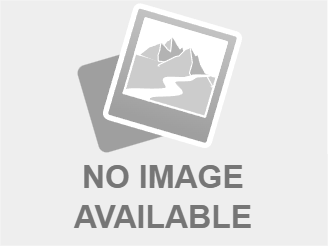
Featured Posts
-
Karate Kid Legend Of The Karate Kid Critics Praise Jackie Chan And Ralph Macchios Performances
May 23, 2025 -
Freepoint Eco Systems And Ing Partner On Project Finance Initiative
May 23, 2025 -
Vybz Kartel Electrifies Brooklyn With Sold Out Concert Series
May 23, 2025 -
Bangladesh Cruise To Victory In Second Test Mehidys Bat And Ball Dominate
May 23, 2025 -
Cat Deeley Shares Emotional Reason Behind Funeral Absence On This Morning
May 23, 2025
Latest Posts
-
Macaulay Culkin And Kieran Culkin Mothers Alleged Financial Hardship Amidst Sons Wealth
May 23, 2025 -
Macaulay And Kieran Culkins Mothers Financial Struggle A Report
May 23, 2025 -
Official Kieran Culkin To Play Caesar Flickerman In The Hunger Games Sunrise On The Reaping
May 23, 2025 -
The Hunger Games Prequel Kieran Culkin Cast As Caesar Flickerman
May 23, 2025 -
Kieran Culkin Confirmed For Caesar Flickerman Role In Hunger Games Prequel
May 23, 2025