Automated Visual Inspection Of Lyophilized Vials: Challenges And Solutions
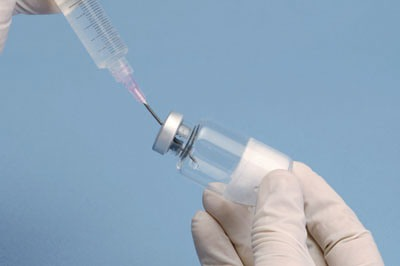
Table of Contents
H2: Challenges in Automated Visual Inspection of Lyophilized Vials
Lyophilization, a process that removes water from a product through freezing and sublimation, creates unique challenges for automated visual inspection. The resulting product, often stored in vials, presents a range of visual characteristics that complicate automated detection of defects.
H3: Variability in Lyophilized Product Appearance
The appearance of lyophilized cakes within vials is inherently variable. This variability makes consistent defect detection incredibly difficult.
- Examples of visual defects: Cracks, bubbles, incomplete lyophilization, discoloration, particulate matter, and collapse.
- Difficulties in consistent defect detection: Subtle variations in cake morphology, density, and color make it challenging to establish clear thresholds for defect identification.
- Impact on automated inspection systems: Inconsistencies require highly adaptable algorithms capable of handling diverse visual presentations of the same defect type. A system optimized for one type of cake may misidentify defects in another.
H3: Lighting and Image Acquisition Challenges
Obtaining clear, consistent images of lyophilized vials is crucial for accurate defect detection, but this is hampered by several factors:
- Specific lighting issues: Glare from the vial surface, shadows cast by the cake, and variations in vial clarity caused by inconsistencies in glass manufacturing.
- Types of cameras and their limitations: Standard cameras may struggle to capture sufficient detail in low-light conditions or with highly reflective surfaces. The choice of camera sensor, lighting angle and intensity greatly affects the quality of the captured image.
- Impact of lighting and image quality on accurate defect detection: Poor image quality leads to missed defects (false negatives) or misidentification of harmless variations as defects (false positives).
H3: Software and Algorithm Limitations
Developing robust algorithms for automated defect detection in lyophilized vials presents a significant challenge.
- Types of algorithms used: Traditional computer vision algorithms, machine learning (ML), and artificial intelligence (AI) techniques.
- Limitations of current algorithms: Existing algorithms may struggle with the inherent variability in lyophilized product appearance, leading to inaccuracies.
- False positives/negatives: The system may flag acceptable variations as defects (false positives), leading to unnecessary product rejection, or fail to detect actual defects (false negatives), resulting in compromised product quality. This emphasizes the need for sophisticated algorithms capable of nuanced defect classification.
H3: High Throughput Requirements and Speed
Pharmaceutical production demands high-speed inspection to maintain efficient manufacturing processes.
- Throughput expectations in pharmaceutical manufacturing: Automated systems must inspect thousands of vials per hour to meet production targets.
- Speed vs. accuracy trade-offs: Balancing the need for speed with the requirement for accurate defect detection is a major challenge. Faster processing can compromise accuracy.
- The need for optimized hardware and software: Optimized hardware, including high-resolution cameras and fast processors, coupled with sophisticated, streamlined software is crucial to achieve both high-speed and high-accuracy inspection.
H2: Solutions for Enhancing Automated Visual Inspection of Lyophilized Vials
Addressing the challenges outlined above requires innovative solutions that leverage advanced technologies and data-driven approaches.
H3: Advanced Imaging Techniques
Emerging imaging techniques offer substantial improvements in defect detection capabilities.
- Specific examples of advanced imaging technologies and their advantages: Hyperspectral imaging provides spectral information beyond the visible range, enabling the detection of subtle variations in chemical composition and physical properties. Multispectral imaging enhances the spectral information obtained in comparison with traditional imaging techniques.
- How these technologies overcome the limitations of traditional imaging: These technologies can overcome challenges posed by variations in lighting and the subtlety of certain defects.
H3: AI and Machine Learning Applications
AI and ML are revolutionizing automated visual inspection.
- Examples of AI/ML algorithms used: Deep learning algorithms, particularly convolutional neural networks (CNNs), are highly effective for image classification and object detection.
- Their benefits in defect detection and classification: AI/ML algorithms can learn to recognize subtle defects, adapt to variations in product appearance, and improve accuracy over time through continuous training.
- How these technologies improve the robustness and adaptability of inspection systems: AI-powered systems are more robust and less prone to false positives or negatives compared to traditional rule-based systems.
H3: Optimized Lighting and Hardware
Careful consideration of lighting and camera systems significantly improves image quality.
- Types of lighting: Structured lighting, polarization techniques, and specialized LED lighting can minimize glare and shadows.
- Camera specifications: High-resolution cameras with advanced sensors are crucial for capturing fine details.
- Considerations for camera placement: Optimizing camera positioning and angle can minimize reflections and maximize image clarity.
H3: Improved Data Management and Analysis
Efficient data management and analysis are crucial for continuous improvement.
- Data storage solutions: Cloud-based storage allows for efficient storage and retrieval of large datasets generated during inspection.
- Data analytics techniques: Statistical process control (SPC) charts and other data visualization tools help identify trends and patterns in defect rates.
- Use of data for process improvement: Data analysis can identify areas for improvement in the lyophilization process, leading to fewer defects and reduced waste.
3. Conclusion:
Automated visual inspection of lyophilized vials faces significant challenges, mainly related to product variability, imaging difficulties, algorithm limitations, and the need for high throughput. However, advanced imaging technologies, AI/ML, optimized hardware, and robust data analysis techniques offer effective solutions. Accurate and efficient automated visual inspection is paramount for maintaining product quality, complying with stringent regulatory standards, and minimizing financial losses associated with product defects. Invest in advanced automated visual inspection systems to enhance your lyophilized vial quality control and ensure the delivery of safe and effective medications to patients. Learn more about the latest advancements in automated visual inspection of lyophilized vials and improve your pharmaceutical manufacturing process.
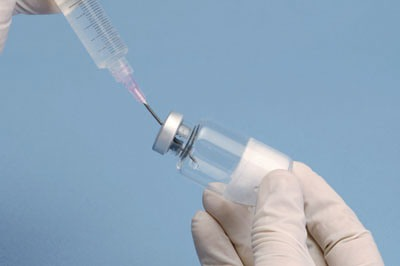
Featured Posts
-
Nba Sixth Man Of The Year Payton Pritchard Makes History For The Celtics
May 11, 2025 -
Stellantis Nears Ceo Decision American Executive A Leading Candidate
May 11, 2025 -
Ligue Des Champions Mueller Decisif Pour Le Bayern Contre L Inter En Quarts
May 11, 2025 -
North American Automakers Uk Trade Deal Worries Underplayed By White House
May 11, 2025 -
5 Key Dos And Don Ts To Succeed In The Private Credit Industry
May 11, 2025