Challenges And Advancements In Automated Visual Inspection Systems For Lyophilized Vials
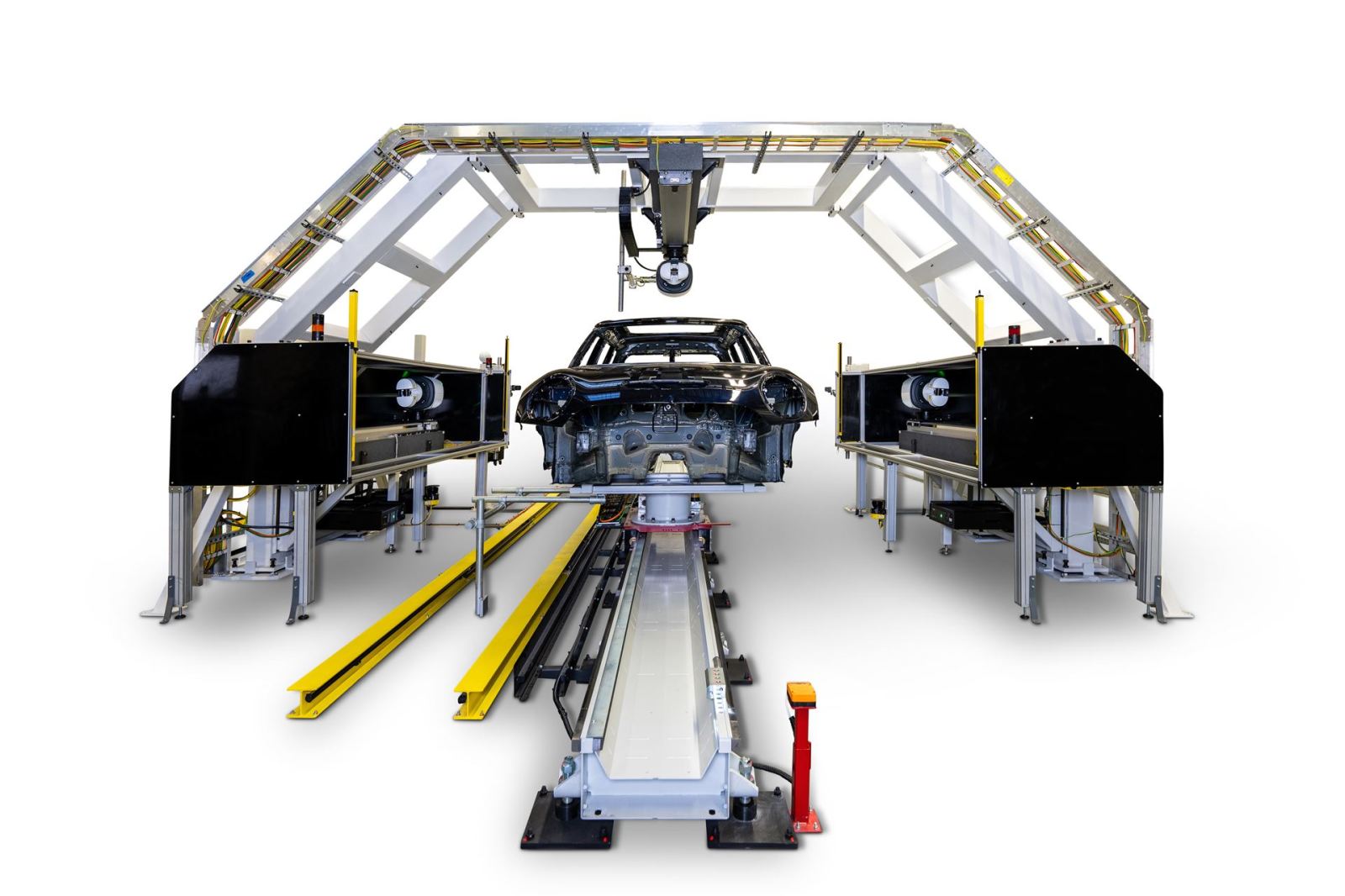
Table of Contents
Challenges in Automated Visual Inspection of Lyophilized Vials
The automated visual inspection of lyophilized vials presents unique challenges due to the inherent nature of the lyophilization process and the characteristics of the product itself.
Variability in Lyophilization Processes
The lyophilization process, also known as freeze-drying, can result in variations in the final product that complicate automated inspection. These variations significantly impact the appearance of the lyophilized cake within the vial.
- Variations in cake formation: The cake's shape, density, and texture can vary, making consistent automated defect detection difficult. Slight inconsistencies in the cake's appearance can be misinterpreted as defects by less sophisticated AVIS systems.
- Collapse and residual moisture: Partial collapse of the lyophilized cake or the presence of residual moisture can affect its visual characteristics, leading to false positives or missed defects. This requires sophisticated algorithms to differentiate between acceptable variations and actual defects.
- Subtle defects: Identifying subtle defects like hairline cracks or fissures in the lyophilized cake requires high-resolution imaging and advanced image processing algorithms. These tiny defects can be easily missed by the human eye, hence the need for highly sensitive AVIS for lyophilized vials.
Dealing with Reflections and Shadows
The glass vials and the lyophilized cake itself create significant challenges for automated visual inspection due to reflections and shadows. These visual artifacts can obscure defects, making accurate detection extremely difficult.
- Light reflections: The smooth surface of the glass vial can cause reflections of the light source, masking defects located beneath. Specialized lighting techniques are crucial to minimize these reflections and enhance contrast.
- Shadowing effects: The shape and position of the lyophilized cake can cast shadows, obscuring potential defects within the shadowed areas. Advanced algorithms are needed to compensate for these shadows and reconstruct a complete image.
- Glass transparency: The transparent nature of the glass vial adds complexity, as the AVIS must differentiate between defects and the vial itself. Precise algorithms are needed to analyze the light transmission through the glass and identify potential flaws.
High Throughput Requirements
Pharmaceutical production lines operate at high speeds, demanding that AVIS for lyophilized vials keep pace without compromising accuracy. This necessitates a balance between speed and accuracy, which is a considerable technological challenge.
- Speed vs. accuracy: Increasing the inspection speed can compromise the accuracy of defect detection. Finding the optimal balance between these two factors is crucial for efficient manufacturing.
- System downtime: Any downtime for maintenance, calibration, or system failures significantly impacts production output. Therefore, AVIS systems for lyophilized vials must be highly reliable and robust.
- Meeting production targets: Pharmaceutical manufacturing requires high throughput to meet market demands. AVIS must be capable of handling large volumes of vials without compromising the quality of inspection.
Advancements in Automated Visual Inspection Systems for Lyophilized Vials
Despite the challenges, significant advancements are transforming the capabilities of Automated Visual Inspection Systems for lyophilized vials.
Improved Imaging Technologies
Significant progress in imaging technology is improving the accuracy and sensitivity of AVIS for lyophilized vials.
- High-resolution cameras: Advanced high-resolution cameras capture fine details of the lyophilized cake, enabling the detection of previously undetectable defects. This significantly improves the sensitivity of the inspection process.
- Multi-spectral imaging: Using different wavelengths of light allows for the detection of defects that are invisible to the naked eye or standard cameras. This approach enhances the ability to identify subtle variations in the lyophilized cake.
- 3D imaging: Three-dimensional imaging provides a comprehensive view of the vial and its contents, allowing for the detection of defects from various angles and perspectives. This overcomes limitations inherent in 2D imaging systems.
Advanced Image Processing Algorithms
Sophisticated image processing algorithms are crucial for interpreting the visual data obtained from high-resolution cameras.
- Machine learning and AI: Machine learning and artificial intelligence (AI) algorithms are trained to recognize and classify defects with increasing accuracy. The algorithms learn from vast datasets of images, enhancing their ability to differentiate between defects and normal variations.
- Deep learning models: Deep learning models, a subset of machine learning, improve their performance with increased data, continuously refining their ability to detect defects. This self-improving nature leads to greater sensitivity and specificity.
- Addressing challenges: Algorithms are constantly being developed to address the specific challenges of reflections, shadows, and variations in the lyophilization process. These solutions refine the ability of AVIS to deal with complex visual artifacts.
Integration with Production Lines
Seamless integration with existing production lines is essential for maximizing the efficiency of AVIS for lyophilized vials.
- Streamlined integration: AVIS systems are designed for seamless integration into existing production lines, minimizing disruption to the manufacturing process. This reduces downtime and maintains production efficiency.
- Automated data logging: Automated data logging and reporting provide comprehensive quality control data, enabling tracking of defects and identifying trends. This allows for proactive measures to improve the lyophilization process.
- Real-time defect analysis: Real-time defect analysis allows for immediate corrective actions, preventing defective products from reaching the market. This immediate feedback loop improves overall product quality and efficiency.
Conclusion
Automated Visual Inspection Systems for lyophilized vials are crucial for ensuring product quality and safety in the pharmaceutical industry. While challenges remain in addressing the complexities of lyophilized product inspection, significant advancements in imaging technologies and image processing algorithms are leading to more reliable and efficient AVIS solutions. The ongoing development of AI and machine learning will further enhance the accuracy and speed of these systems. To learn more about the latest advancements in AVIS for Lyophilized Vials and how they can benefit your pharmaceutical manufacturing process, contact us today. Invest in superior quality control with advanced Automated Visual Inspection Systems for Lyophilized Vials.
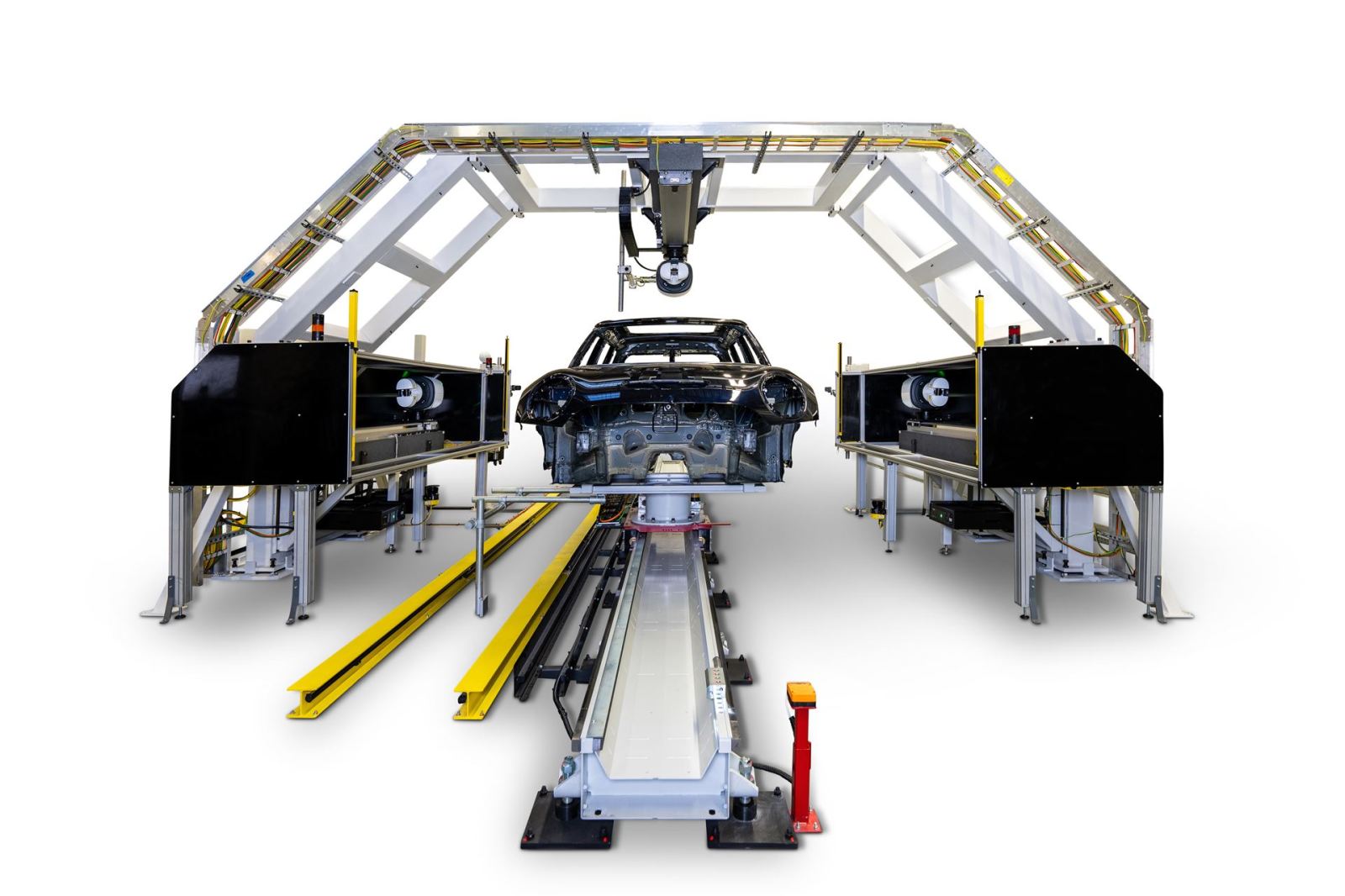
Featured Posts
-
Lowry Pushes For Victory At Valspar Championship
May 12, 2025 -
Regalo Presidencial Tres Toros Partiendo Hacia China Desde Uruguay
May 12, 2025 -
Lowrys Encouraging Words For Mc Ilroy Post Masters Highlight Their Strong Bond
May 12, 2025 -
Payton Pritchards New Converse Shoe Deal Details And Impact
May 12, 2025 -
Masazystka Ujawnia Szokujace Spotkanie Z Ksieciem Andrzejem Reakcja Rodziny Krolewskiej
May 12, 2025
Latest Posts
-
Mtv Cribs A Tour Of Stunning Beachfront Homes
May 12, 2025 -
Unexpected Elimination In The Challenge Season 41 Spoilers Inside
May 12, 2025 -
Challenge Season 41 Spoiler Alert Unexpected Twist And Veteran Survival
May 12, 2025 -
Stream Over 100 Mtv Unplugged Performances Complete Episode Guide
May 12, 2025 -
Mtv Unplugged Full List Of 100 Episodes Available Now
May 12, 2025