Enhanced Automated Visual Inspection For Lyophilized Vials: A Practical Guide
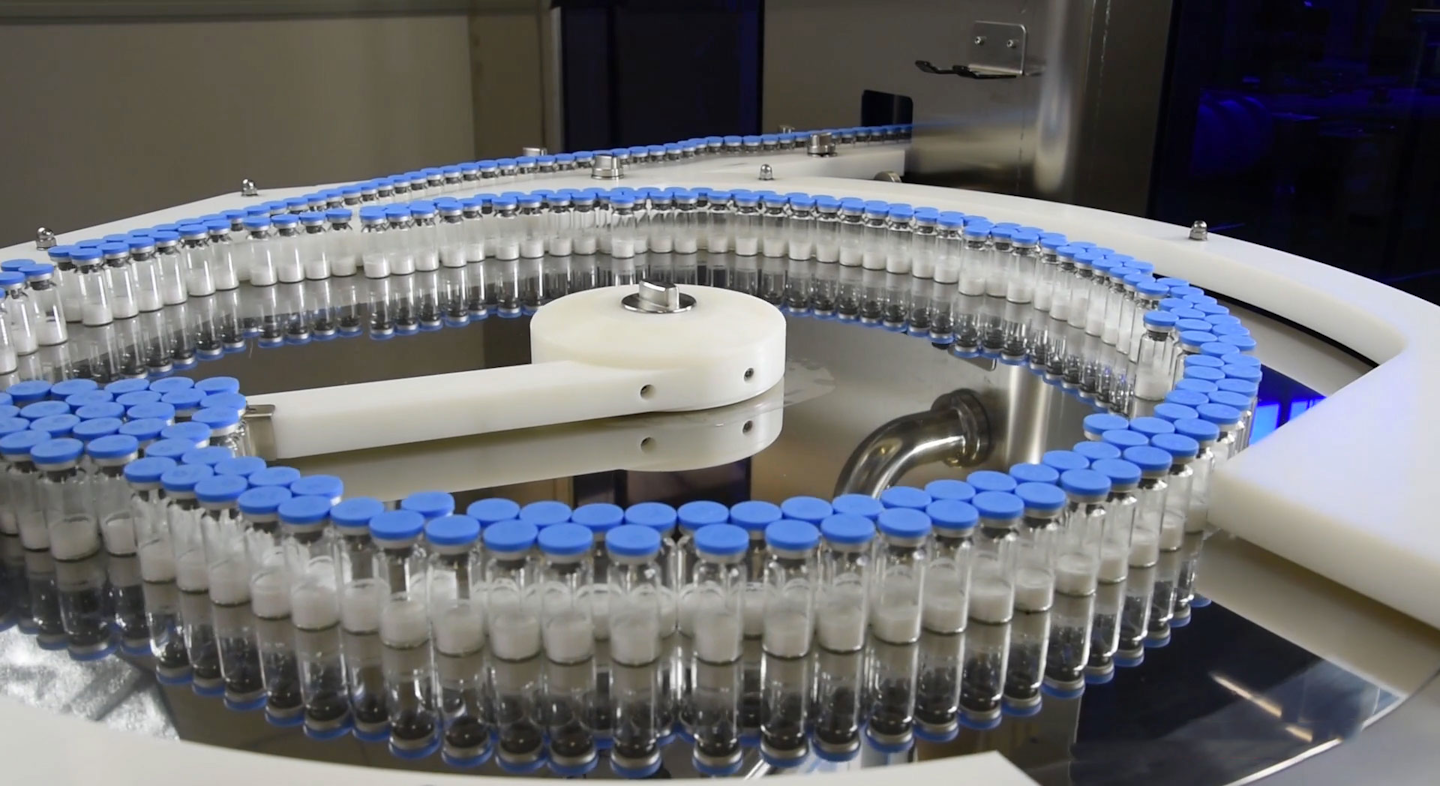
Table of Contents
Benefits of Automated Visual Inspection over Manual Methods
Manual inspection of lyophilized vials is time-consuming, prone to human error, and ultimately, less efficient. Automated visual inspection systems offer a significant upgrade, providing numerous advantages:
Increased Throughput and Efficiency:
- Eliminates human error and fatigue: Automated systems tirelessly inspect vials, eliminating fatigue-related errors common in manual inspection. This leads to significantly faster inspection times, crucial for high-volume production.
- Handles high-volume production runs: Automated systems are designed to handle the throughput demands of large-scale lyophilization processes without compromising accuracy. They can consistently inspect thousands of vials per hour, significantly increasing productivity.
- Frees up human inspectors for more complex tasks: By automating routine visual inspections, human inspectors can focus on more complex tasks requiring expertise and judgment, optimizing workforce utilization and improving overall efficiency.
Enhanced Accuracy and Consistency:
- Objective assessments: Unlike manual inspection, which is susceptible to subjective biases, automated systems provide objective and consistent assessments of vial quality. This ensures uniform quality control across all batches.
- Consistent defect detection: Automated systems consistently detect defects, minimizing variations that can occur in manual inspection due to fatigue or changing environmental conditions. This leads to improved identification of subtle defects that may be missed by the human eye.
- Improved detection of subtle defects: Advanced imaging techniques and AI algorithms allow for the detection of minute defects, such as micro-cracks, particulate matter, or inconsistencies in fill level, which can compromise product integrity and patient safety.
Reduced Operational Costs:
- Lower labor costs: Automated systems significantly reduce labor costs associated with manual inspection, offering a substantial return on investment over time.
- Minimized product loss: Improved defect detection minimizes product loss due to the rejection of defective vials, saving both time and resources.
- Improved overall efficiency: The increased speed and accuracy of automated inspection lead to improved overall efficiency, resulting in significant cost savings across the entire lyophilization process.
Key Technologies in Automated Visual Inspection Systems for Lyophilized Vials
Modern automated visual inspection systems for lyophilized vials leverage advanced technologies to achieve superior accuracy and efficiency:
High-Resolution Imaging:
- Advanced cameras: These systems utilize high-resolution cameras capable of capturing detailed images of vial contents and exterior, providing a comprehensive assessment of product integrity.
- Various lighting techniques: Different lighting techniques, such as dark field and bright field illumination, are employed to optimize defect visualization, enhancing the visibility of subtle imperfections.
- Image enhancement algorithms: Advanced image processing algorithms enhance contrast and clarity, improving the accuracy of defect detection and minimizing false positives.
AI and Machine Learning for Defect Detection:
- Advanced algorithms: AI and machine learning algorithms are trained to identify a wide range of defects, including particulate matter, cracks, seal integrity issues, and variations in fill level.
- Continuous learning: These systems continuously learn and adapt to evolving quality standards and new types of defects, ensuring ongoing accuracy and effectiveness.
- Data analytics integration: Integration with data analytics platforms allows for real-time monitoring of inspection data, enabling proactive identification of trends and potential process improvements.
Robotic Handling and Integration:
- Automated vial handling: Robotic systems handle vials gently and efficiently, minimizing the risk of damage during inspection and ensuring smooth integration with upstream and downstream processes.
- Seamless line integration: Automated systems integrate seamlessly with existing production lines and automated packaging systems, creating a fully automated workflow.
- Improved traceability: Automated data logging and tracking provide improved traceability of inspected vials, enhancing quality control and regulatory compliance.
Implementing Enhanced Automated Visual Inspection: Practical Considerations
Successful implementation of automated visual inspection systems requires careful planning and consideration:
System Selection and Validation:
- System capabilities: Careful consideration must be given to the system’s capabilities, ensuring it meets the specific needs of the lyophilization process and the types of defects that need to be detected.
- Validation procedures: Rigorous validation procedures are essential to ensure the system's accuracy, reliability, and compliance with regulatory requirements.
- Regulatory compliance: Compliance with regulations like FDA 21 CFR Part 11 is paramount, ensuring the integrity and auditability of inspection data.
Training and Personnel:
- Operator training: Thorough training is necessary for personnel responsible for operating and maintaining the system, ensuring proper use and troubleshooting capabilities.
- Standard operating procedures (SOPs): Well-defined SOPs for system operation and data management are essential for consistent performance and data integrity.
- Performance monitoring: Ongoing monitoring and assessment of system performance are critical for identifying and addressing potential issues.
Ongoing Maintenance and Calibration:
- Regular maintenance: Regular preventive maintenance is essential to ensure optimal performance and minimize downtime, extending the lifespan of the system.
- Calibration procedures: Regular calibration procedures are critical for maintaining the accuracy and precision of the system’s measurements.
- Preventive maintenance programs: Implementing a comprehensive preventive maintenance program minimizes the risk of malfunctions and ensures consistent system performance.
Conclusion
Implementing enhanced automated visual inspection for lyophilized vials offers significant advantages in terms of speed, accuracy, and cost-effectiveness. By leveraging advanced technologies such as high-resolution imaging and AI-powered defect detection, pharmaceutical manufacturers can ensure the highest levels of product quality and compliance. This guide provides a practical framework for choosing, implementing, and maintaining these systems. Investing in advanced automated visual inspection is crucial for maintaining a competitive edge in the pharmaceutical industry. Start optimizing your lyophilized vial inspection process today by exploring the options available in enhanced automated visual inspection systems.
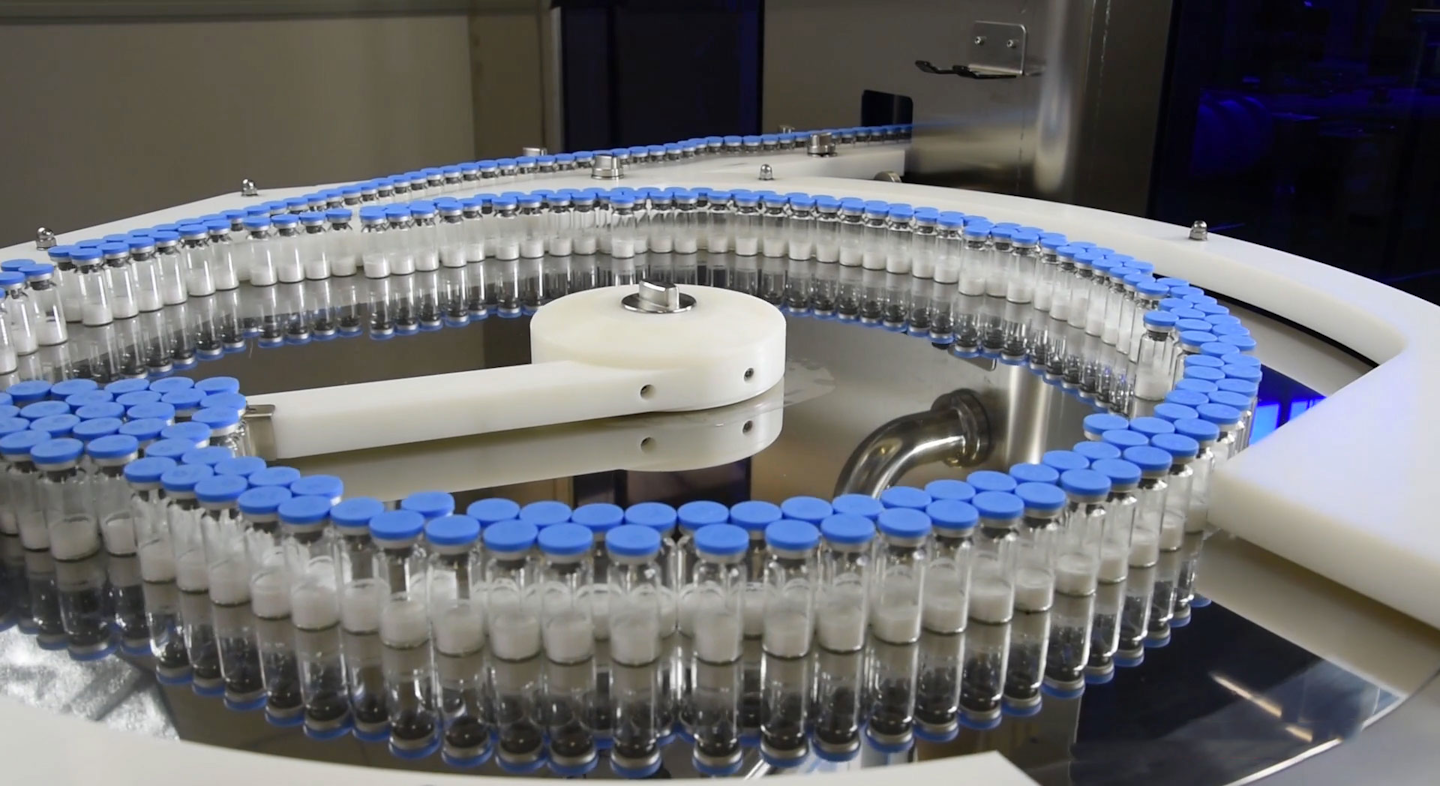
Featured Posts
-
Alex Winters Lost Mtv Years The Sketch Comedy That Preceded Freaked
May 12, 2025 -
Analyzing The Leading Contenders To Succeed Pope Francis
May 12, 2025 -
Experiences Of Meeting Shane Lowry Fan Stories
May 12, 2025 -
Bayern Munichs Future Without Mueller Fan Reactions And Transfer Speculation
May 12, 2025 -
Updated Injury Report Yankees Vs Brewers March 27 30
May 12, 2025
Latest Posts
-
Unexpected Elimination In The Challenge Season 41 Spoilers Inside
May 12, 2025 -
Challenge Season 41 Spoiler Alert Unexpected Twist And Veteran Survival
May 12, 2025 -
Stream Over 100 Mtv Unplugged Performances Complete Episode Guide
May 12, 2025 -
Mtv Unplugged Full List Of 100 Episodes Available Now
May 12, 2025 -
Mtv Cancels 2025 Movie And Tv Awards Ceremony
May 12, 2025