F-35 Inventory Management Failures Highlighted In Pentagon Audit
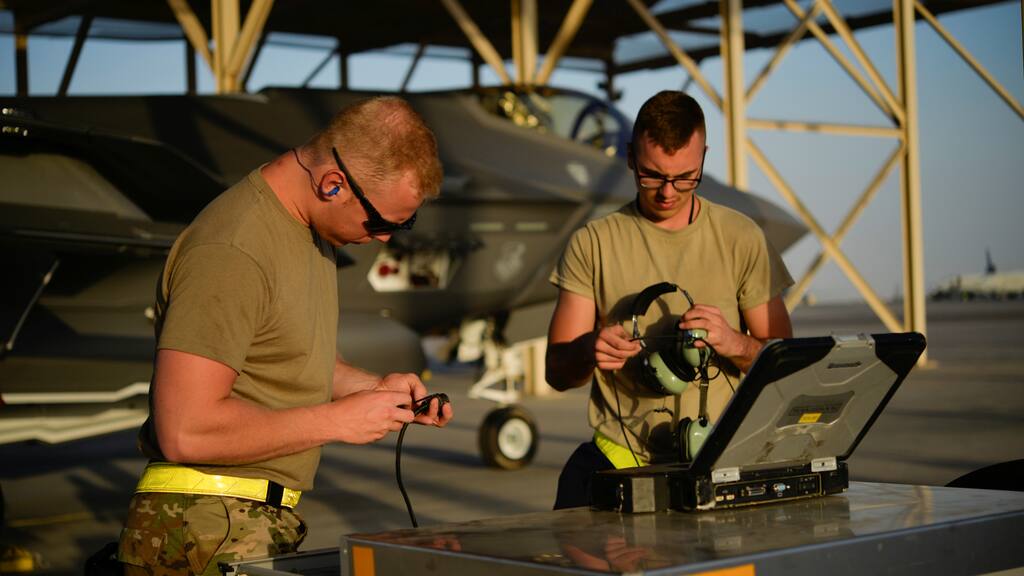
Table of Contents
Significant Discrepancies in F-35 Part Tracking
The audit uncovered alarming discrepancies in the tracking of F-35 spare parts, highlighting a critical weakness in the program's logistics system. The scale of the problem is substantial, with reports indicating significant numbers of missing parts, inaccurate inventory records, and substantial delays in procurement. This inadequate F-35 spare parts management directly impacts the ability to maintain and repair the aircraft fleet effectively.
-
Specific examples: The audit cited instances where crucial engine components were reported as "in stock" when they were, in fact, missing, leading to extended periods of aircraft downtime. Other examples include discrepancies in the number of reported and actual small but critical parts like sensors and wiring harnesses.
-
Impact on maintenance: These inaccuracies lead to significant delays in F-35 maintenance schedules, reducing the fleet's operational readiness. Mechanics waste valuable time searching for parts that are incorrectly recorded, leading to increased maintenance costs and decreased aircraft availability.
-
Cost implications: The financial implications of these discrepancies are staggering. The cost of lost flight hours, extended maintenance periods, and the need for expedited part procurement significantly increase the overall cost of operating the F-35 fleet. This inefficient F-35 inventory management translates directly into increased taxpayer burden.
-
Root causes: The audit points to several root causes, including poor data entry practices, a lack of a real-time, integrated inventory tracking system, and insufficient training for personnel responsible for managing the F-35 supply chain. Ineffective supply chain management is a major contributor to these failures.
Challenges in Managing the Global F-35 Supply Chain
Managing the global supply chain for the F-35 presents unique and complex challenges. The aircraft's advanced technology requires parts sourced from numerous international suppliers, adding layers of complexity to inventory tracking and logistics. This global network for F-35 parts procurement increases the vulnerability of the system.
-
International collaboration: The international collaboration involved in F-35 production, with participation from several countries, creates complexities in communication, standardization, and logistics. Differences in regulations and customs procedures further hinder efficient part sourcing and transportation.
-
Part sourcing, transportation, and customs: Sourcing parts from multiple international locations introduces delays and potential disruptions due to transportation issues, customs clearances, and potential geopolitical instability. These complications significantly impact the timely delivery of crucial F-35 spare parts.
-
Supply chain vulnerabilities: The geographically dispersed nature of the supply chain makes it vulnerable to disruptions from various factors, including natural disasters, political instability, and even pandemics. This vulnerability highlights the need for a more resilient and adaptable F-35 inventory management strategy.
-
Security concerns: The secure tracking and handling of sensitive F-35 parts are of paramount importance. The audit raises concerns about the potential for theft or unauthorized access to these crucial components, emphasizing the need for enhanced security measures throughout the supply chain.
Impact on F-35 Operational Readiness and Mission Capability
The failures in F-35 inventory management directly translate into reduced operational readiness and compromised mission capability. The lack of readily available parts limits the number of aircraft that can be deployed at any given time, impacting the overall effectiveness of the fleet.
-
Flight hours and operational availability: Delays in maintenance and repairs caused by inventory management issues directly reduce the number of flight hours available for training and operational missions. This directly impacts the readiness of the F-35 fleet for deployment.
-
Increased maintenance costs and downtime: The inefficiencies in the system lead to increased maintenance costs due to longer downtime, expedited shipping, and the need for additional personnel to address inventory discrepancies.
-
Impact on national security: A compromised F-35 fleet, due to poor inventory management, directly impacts national security and defense capabilities, particularly in the context of rapid response scenarios.
-
Pilot training and readiness: Reduced flight hours due to maintenance delays also negatively impact pilot training and overall readiness, further diminishing the operational effectiveness of the F-35 fleet.
Proposed Solutions and Recommendations
Addressing these critical F-35 inventory management failures requires a multi-faceted approach involving technological upgrades, improved data management, and enhanced international collaboration.
-
Advanced inventory management systems: Implementing advanced technologies, such as RFID (Radio-Frequency Identification) tagging and blockchain technology, can significantly improve real-time tracking and accuracy of F-35 spare parts. This improved tracking system is crucial for effective F-35 inventory management.
-
Improved data management: Investing in robust, integrated data management systems is critical to ensuring accurate inventory records and real-time visibility into the supply chain. This enhanced data management, along with improved data entry practices, is paramount.
-
Supply chain optimization: Streamlining the global supply chain through enhanced collaboration with international partners and the implementation of optimized logistics processes is necessary for efficient F-35 parts procurement and delivery.
-
Increased investment: Increased investment in logistics infrastructure and maintenance personnel is crucial to support effective F-35 inventory management and ensure the fleet's readiness.
Conclusion
The Pentagon audit's findings highlight the severity of F-35 inventory management failures and their far-reaching consequences on operational readiness, national security, and overall program cost. The lack of accurate inventory tracking, coupled with the complexities of a global supply chain, has created a critical vulnerability in the F-35 program. Addressing these issues requires immediate and decisive action. We must learn from these failures and invest in robust solutions, from implementing advanced inventory management software to optimizing the global supply chain. The future effectiveness of the F-35 fleet hinges on significantly improving F-35 inventory management practices and preventing future failures. Further investigation and the implementation of comprehensive solutions are crucial for maintaining national security and ensuring the long-term success of this vital program.
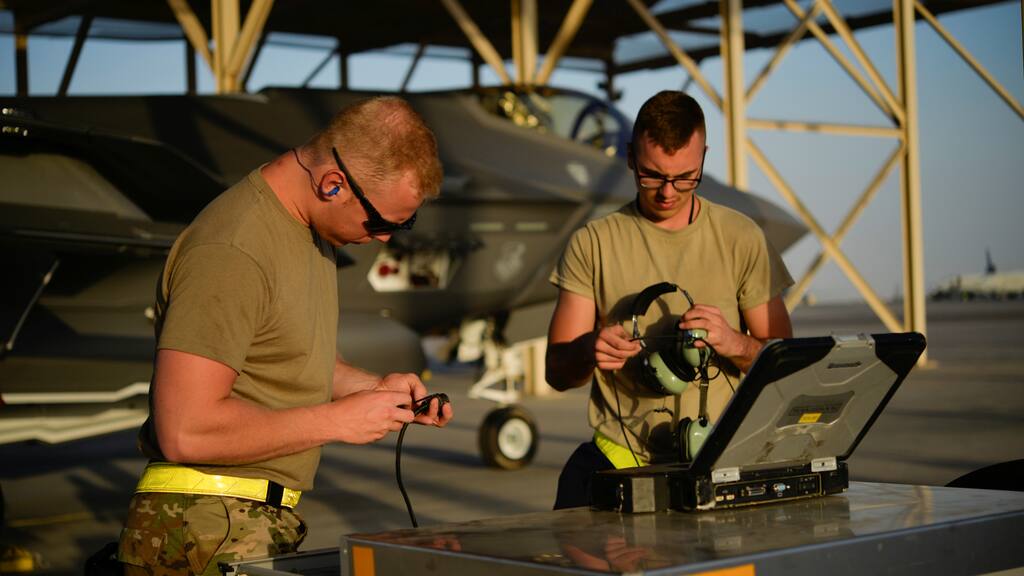
Featured Posts
-
Canadian Staycations Boom Airbnb Bookings Up 20
May 01, 2025 -
Snl Bowen Yang Wanted Lorne Michaels To Replace Him Playing Jd Vance
May 01, 2025 -
7 2025 12
May 01, 2025 -
Xrp Ripple Price Below 3 Investment Analysis And Risks
May 01, 2025 -
Aaron Judge Paul Goldschmidt Key Players In Yankees Series Win
May 01, 2025