Improving Automated Visual Inspection Of Lyophilized Vials: A Practical Guide
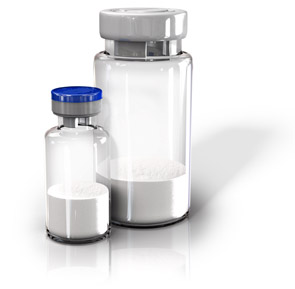
Table of Contents
Challenges in Manual Visual Inspection of Lyophilized Vials
Manual visual inspection of lyophilized vials relies heavily on human inspectors, who visually examine each vial for defects like cracks, particulate matter, or insufficient fill. This method suffers from several inherent limitations:
- Human Error and Subjectivity: Inspector fatigue, inconsistent performance, and subjective interpretation of defects lead to significant variability and potential errors. One inspector might deem a minor imperfection acceptable while another flags it as a critical defect. This subjectivity can result in inconsistent quality control and increased risk of releasing defective products.
- High Costs: Manual inspection is labor-intensive and requires a large workforce, resulting in high labor costs and significant overhead. The need for extensive training and rigorous quality control procedures further adds to the expense.
- Production Bottlenecks: The speed of manual inspection is inherently limited, creating a bottleneck in the production process and hindering output. This delay can significantly impact overall manufacturing efficiency and timelines.
In short:
- High labor costs
- Increased risk of human error
- Subjectivity in defect classification
- Bottlenecks in production
- Increased risk of product recalls due to undetected defects
Benefits of Automated Visual Inspection Systems
Automated visual inspection systems offer a superior alternative to manual methods, providing numerous advantages:
- Increased Speed and Throughput: Automated systems can inspect vials significantly faster than human inspectors, dramatically increasing throughput and production efficiency. This allows manufacturers to process larger volumes of vials in a shorter time frame.
- Improved Accuracy and Consistency: Automated systems consistently apply predefined inspection criteria, eliminating human subjectivity and reducing errors. The objective nature of automated defect detection ensures higher accuracy and greater consistency in quality control.
- Reduced Costs: While initial investment can be significant, automated systems ultimately reduce long-term costs by lowering labor expenses and minimizing the risk of costly product recalls associated with human error. They also improve overall efficiency and reduce waste.
Key Advantages:
- Increased throughput
- Improved accuracy and consistency
- Reduced labor costs
- Enhanced quality control
- Objective defect detection
Key Technologies for Automated Visual Inspection of Lyophilized Vials
Several advanced technologies underpin automated visual inspection of lyophilized vials:
- Machine Vision Systems: These systems utilize cameras, lenses, and lighting to capture high-resolution images of vials. Sophisticated algorithms analyze these images to detect defects based on pre-programmed criteria. Different camera types (e.g., monochrome, color) and lighting techniques (e.g., backlighting, dark-field illumination) are selected based on the specific defects to be detected.
- AI-powered Defect Detection: Artificial intelligence (AI) and machine learning (ML) algorithms are increasingly used to improve the accuracy and speed of defect detection. These algorithms can learn to identify complex defects and adapt to variations in vial appearance. Deep learning models, in particular, have shown great promise in automatically classifying subtle defects that might be missed by human inspectors.
- Hyperspectral Imaging: This advanced technique captures images across a wide range of wavelengths, providing detailed spectral information about the vial's contents and structure. This enables the detection of defects invisible to the human eye or standard machine vision systems, such as subtle variations in the lyophilized cake.
Implementing and Optimizing Automated Visual Inspection
Successfully implementing an automated visual inspection system requires careful planning and execution:
- System Selection: Selecting the appropriate system requires careful consideration of factors such as throughput requirements, the types of defects to be detected, budget constraints, and integration with existing manufacturing processes. A thorough needs assessment is crucial.
- Validation and Qualification: Rigorous validation and qualification procedures are essential to ensure the system's accuracy and reliability. These procedures verify that the system meets the required performance standards and complies with relevant regulations.
- Parameter Optimization: Fine-tuning inspection parameters (e.g., lighting, image processing algorithms, acceptance criteria) is critical to minimize false positives and false negatives. This often involves iterative testing and optimization to achieve optimal performance.
- Integration with Existing Processes: Seamless integration of the automated system with existing manufacturing processes is essential for smooth operation and efficient workflow. This includes consideration of data management, reporting, and potential adjustments to existing workflows.
Future Trends in Automated Visual Inspection of Lyophilized Vials
The field of automated visual inspection is constantly evolving:
- Advanced AI and Deep Learning: The application of advanced AI and deep learning algorithms will continue to enhance the accuracy, speed, and adaptability of automated systems. These algorithms can learn from larger datasets and adapt to increasingly complex defect patterns.
- Integration with PAT Initiatives: Integrating automated visual inspection with other process analytical technologies (PAT) offers the potential for real-time process monitoring and control, further improving product quality and consistency.
- Predictive Maintenance: Data analytics can be used to predict potential equipment failures and optimize maintenance schedules, minimizing downtime and ensuring the continuous operation of the automated inspection system.
Conclusion: Improving Your Automated Visual Inspection of Lyophilized Vials
Implementing automated visual inspection systems for lyophilized vials offers significant advantages, including increased speed, enhanced accuracy, reduced costs, and improved overall quality control. By carefully considering the factors outlined in this guide – from system selection and implementation to optimization and integration – pharmaceutical manufacturers can significantly improve their Automated Lyophilized Vial Inspection processes. Investing in advanced technologies, such as AI-powered defect detection and hyperspectral imaging, will further enhance the efficiency and reliability of Automated Visual Inspection of Lyophilized Vials. To learn more about optimizing your Improving Lyophilized Vial Inspection processes, contact us today for a consultation.
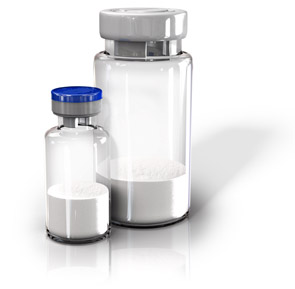
Featured Posts
-
The Baba Yaga Role Your John Wick Las Vegas Adventure
May 11, 2025 -
The Need For Depth Reimagining Asian And Asian American Narratives In Media
May 11, 2025 -
Faber Faces Backlash Over Rejected Coa Volunteer Honours
May 11, 2025 -
New York Yankees Dominate Pittsburgh Pirates Judges Home Run Highlights Win
May 11, 2025 -
Analyzing Holstein Kiels Relegation From The Bundesliga
May 11, 2025