Overcoming Hurdles In Automated Visual Inspection Of Lyophilized Drug Products
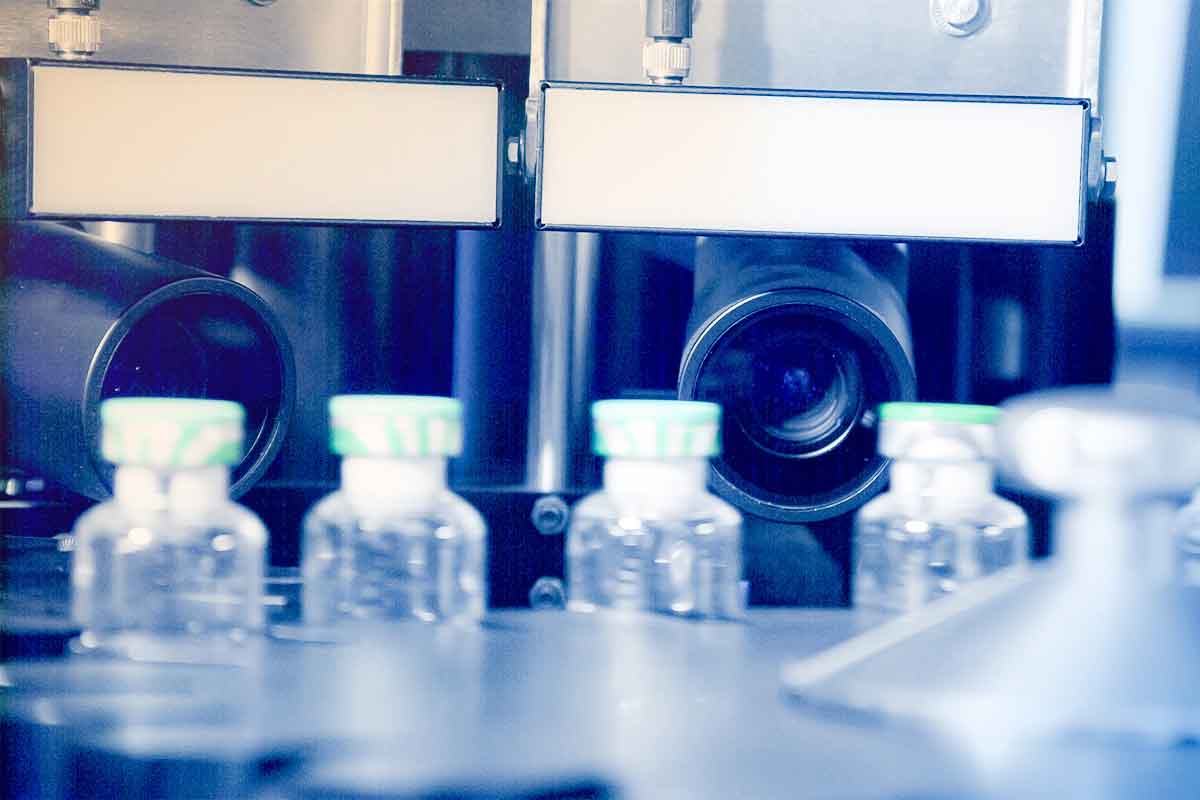
Table of Contents
Challenges in Image Acquisition for Lyophilized Drug Products
The inherent complexities of lyophilized drug products present unique challenges for automated visual inspection. The appearance of the lyophilized cake, the vial itself, and even the lighting conditions all play a role in the success or failure of automated systems.
Variations in Lyophilized Cake Appearance
Lyophilization, or freeze-drying, can result in variations in the appearance of the final drug product. These variations can significantly impact the effectiveness of automated visual inspection systems.
- Cracks and Fissures: These structural imperfections can be difficult to distinguish from acceptable variations in cake structure.
- Collapse: Partial or complete collapse of the lyophilized cake can lead to significant inconsistencies in appearance.
- Surface Texture: Variations in surface texture, such as roughness or pitting, can confound image analysis algorithms.
These variations make it challenging for automated systems to reliably distinguish between acceptable variations and actual defects. Image analysis algorithms must be robust enough to account for this inherent variability to minimize false positives and false negatives. Careful calibration and training of the AVI system using a diverse dataset of lyophilized cakes is crucial for optimal performance.
Lighting and Shadowing Effects
Inconsistent lighting is a major source of error in automated visual inspection. Shadows cast by the vial or the lyophilized cake itself can obscure defects, leading to missed critical quality attributes.
- Vial Orientation: The angle of the vial relative to the light source can significantly affect shadow formation.
- Surface Reflections: Glossy surfaces can create reflections that interfere with image acquisition and analysis.
- Non-Uniform Illumination: Uneven lighting across the vial can lead to inconsistent image quality.
Advanced lighting techniques, such as diffused lighting and multi-angle illumination, are essential to mitigate these effects. Sophisticated image processing algorithms can also be employed to compensate for shadows and reflections, improving the overall accuracy of the inspection. Careful control of the environment and optimized vial handling are crucial for minimizing these challenges.
High-Throughput Demands and System Speed
The pharmaceutical industry demands high-throughput screening capabilities to meet production needs. Automated visual inspection systems must be able to inspect vials at high speeds without compromising accuracy.
- Throughput Optimization: Balancing speed and accuracy is crucial for efficient production.
- Real-time Inspection: Real-time feedback is essential for immediate process adjustments, improving efficiency and reducing waste.
- System Scalability: The system needs to be scalable to accommodate increases in production volume.
The trade-off between speed and accuracy requires careful consideration. Faster inspection may necessitate simplified algorithms which may compromise accuracy. Implementing advanced hardware and software solutions, alongside robust quality control measures, is essential to ensure both high throughput and reliable defect detection.
Advanced Techniques for Improved Automated Visual Inspection
Addressing the challenges of AVI for lyophilized products requires the implementation of advanced techniques in imaging and data analysis.
Advanced Imaging Modalities
Moving beyond traditional 2D imaging can significantly enhance defect detection capabilities.
- Hyperspectral Imaging: This technique captures images across a wide range of wavelengths, providing detailed spectral information about the lyophilized cake. This allows for the detection of subtle variations in composition and structure that are invisible to the naked eye or standard 2D cameras.
- Multispectral Imaging: Similar to hyperspectral imaging, but with fewer wavelengths, multispectral imaging can still provide valuable information for defect detection.
- 3D Imaging: 3D imaging techniques, such as structured light scanning, allow for the creation of three-dimensional models of the lyophilized cake, providing a more complete view of its structure and potential defects.
These advanced imaging modalities provide significantly more data than traditional 2D imaging, leading to more accurate and reliable defect detection. The additional information helps differentiate between acceptable variations and genuine defects.
Artificial Intelligence (AI) and Machine Learning (ML) in AVI
AI and ML are revolutionizing automated visual inspection by enabling the development of more robust and adaptive algorithms.
- Deep Learning: Deep learning algorithms, particularly convolutional neural networks (CNNs), are highly effective in analyzing images and identifying complex patterns.
- Algorithm Optimization: AI/ML allows for continuous optimization of algorithms, improving their accuracy and adaptability to variations in lyophilized cake appearance.
- Defect Classification: AI/ML enables more accurate classification of defects, differentiating between critical and non-critical issues.
By training AI/ML algorithms on large datasets of images, systems can learn to recognize and classify defects with high accuracy, even in the presence of variations in cake appearance and lighting conditions.
Data Analytics and Process Optimization
Data analytics plays a vital role in improving the overall efficiency and effectiveness of the AVI process.
- Process Analytical Technology (PAT): Integrating data from AVI with other process parameters enables better understanding of the lyophilization process.
- Defect Analysis: Analyzing defect data can identify trends and root causes, leading to improvements in process parameters.
- Real-time Feedback: Real-time data analysis provides immediate feedback, enabling process adjustments and prevention of further defects.
By analyzing data collected during AVI, manufacturers can identify areas for process optimization, reducing defects and improving overall product quality.
Validation and Regulatory Compliance
The validation and regulatory compliance of automated visual inspection systems are critical for ensuring the reliability and acceptability of results.
Validation Requirements for Automated Visual Inspection Systems
Thorough validation is essential to demonstrate the accuracy and reliability of the AVI system.
- IQ/OQ/PQ Validation: Installation Qualification (IQ), Operational Qualification (OQ), and Performance Qualification (PQ) are crucial steps to verify the system’s design, operation, and performance.
- Algorithm Validation: Validation of the image analysis algorithms is critical to ensure their accuracy and reliability.
- Data Integrity: Maintaining data integrity throughout the process is crucial for regulatory compliance.
Rigorous validation ensures the system consistently meets predefined performance criteria, providing confidence in the accuracy of the inspection results.
Meeting Regulatory Guidelines
Compliance with regulatory guidelines is paramount.
- FDA Guidelines: The FDA provides guidance on the validation and use of automated inspection systems for pharmaceuticals.
- EMA Guidelines: Similar guidelines are provided by the European Medicines Agency (EMA).
- GMP Compliance: Automated visual inspection systems must adhere to Good Manufacturing Practices (GMP).
Understanding and adhering to these guidelines is critical for ensuring the regulatory acceptability of the AVI system and the resulting data.
Conclusion
Automated visual inspection of lyophilized drug products presents significant challenges, but advancements in imaging techniques, AI, and data analytics are paving the way for more robust and accurate systems. By addressing the hurdles discussed above, the pharmaceutical industry can leverage the benefits of automated visual inspection to improve product quality, increase efficiency, and ensure regulatory compliance. Implementing advanced solutions in automated visual inspection of lyophilized drug products is crucial for maintaining high standards in pharmaceutical manufacturing. Investing in and optimizing your automated visual inspection processes is a key step towards future-proofing your lyophilization operations.
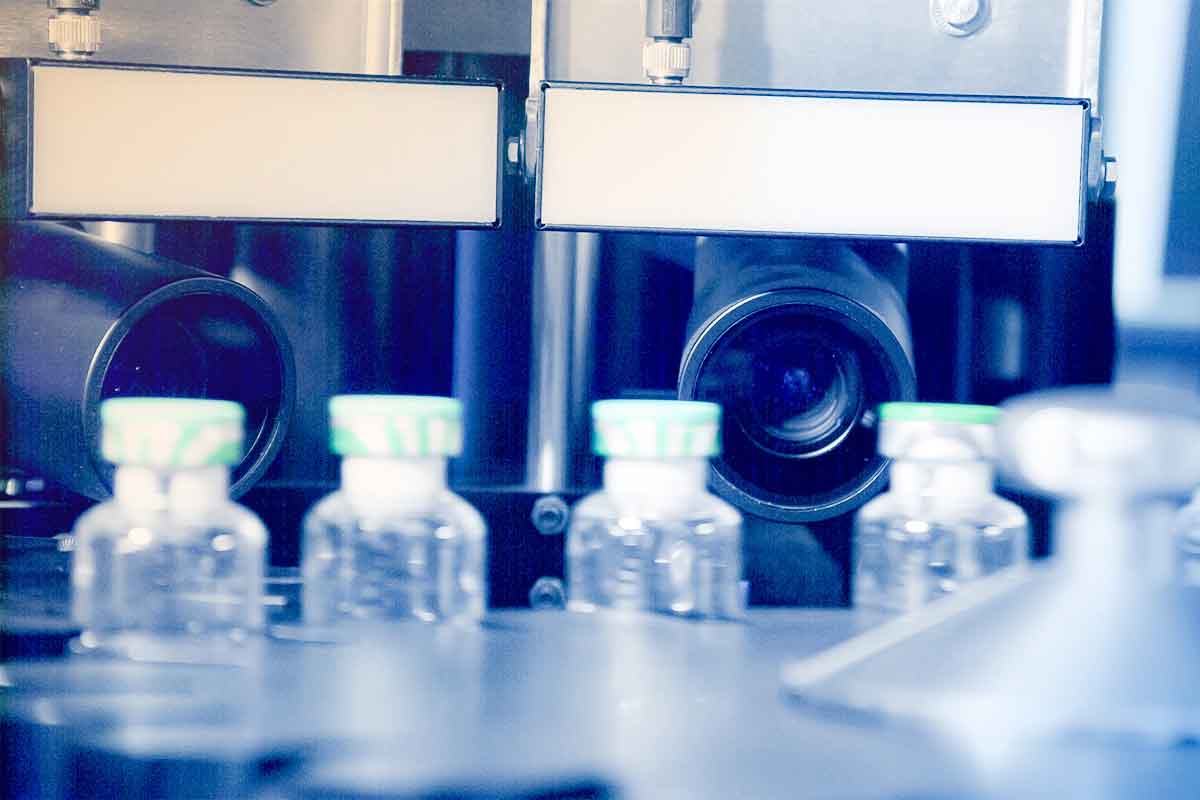
Featured Posts
-
Schandaal Prins Andrew Verjaardagskaarten Aan Xi Jinping En Dubieuze Relaties
May 12, 2025 -
Who Inspired Gatsby Tracing The Real Life Figures Behind The Novel
May 12, 2025 -
Astronauts Extended Space Stay A Cbs News Report
May 12, 2025 -
Ipswich Towns Winning Strategy The Chaplin Influence
May 12, 2025 -
How Fox News Covers Conor Mc Gregor A Detailed Look
May 12, 2025
Latest Posts
-
Pokhudenie Dzhessiki Simpson Podrobnosti Ee Diety I Trenirovok
May 12, 2025 -
Neal Mc Clellands Ill House U Ft Andrea Love House Musics Latest Hit
May 12, 2025 -
Jessica Simpsons Cheetah Print And Blue Fur Coat A Glamorous Airport Look
May 12, 2025 -
From Mtv Cribs A Look At The Architectural Styles Of Celebrity Homes
May 12, 2025 -
Exploring The Lavish Estates Showcased On Mtv Cribs
May 12, 2025