Strategies For Optimizing Automated Visual Inspection Of Lyophilized Vials
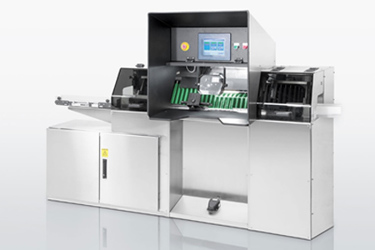
Table of Contents
Choosing the Right Automated Visual Inspection System
Selecting the appropriate automated visual inspection system is paramount for successful implementation. The system's capabilities directly impact inspection efficiency and accuracy, influencing both speed and the detection of critical defects.
Considering System Capabilities
The ideal system must possess several key features:
- High-resolution imaging: Crucial for detecting subtle defects such as minute particulate matter or hairline cracks. Higher resolution translates to greater sensitivity and accuracy in defect detection.
- Advanced algorithms: Sophisticated image analysis algorithms, possibly incorporating machine learning (AI-powered inspection), are vital for identifying complex defects and minimizing false positives and false negatives. These algorithms should be capable of distinguishing between acceptable variations and actual defects.
- High throughput: The system should be able to handle the required volume of vials, ensuring efficient processing and minimizing production bottlenecks. High-throughput screening capabilities are essential for high-volume pharmaceutical manufacturing.
- 3D imaging: This capability allows the system to detect defects hidden in shadows or obscured by the vial's geometry, offering a more comprehensive inspection. 3D imaging significantly improves the detection rate of subtle defects.
- Spectral analysis: This advanced technique uses different wavelengths of light to identify and characterize particulate matter, providing detailed information about the nature and size of contaminants.
These features are crucial elements of any robust automated visual inspection system for lyophilized vial inspection. The choice depends on specific needs and budget.
Integration with Existing Production Lines
Seamless integration with your existing infrastructure is critical. This includes:
- Automated data transfer: The system should seamlessly transfer inspection data to your existing data management systems, such as Manufacturing Execution Systems (MES). This eliminates manual data entry and reduces the risk of errors.
- Real-time monitoring: Real-time monitoring allows for immediate identification of issues and facilitates proactive adjustments to the production process. This minimizes downtime and waste.
- Reduced manual intervention: Automation reduces the need for manual handling, minimizing the risk of contamination and improving overall efficiency. This simplifies the inspection workflow and enhances productivity. The goal is to create a fully integrated lyophilized vial inspection process within your existing production line automation. Effective system integration ensures a smooth and efficient workflow.
Optimizing Image Acquisition and Processing Parameters
Optimizing image acquisition and processing is crucial for maximizing the accuracy and reliability of the automated visual inspection system.
Illumination and Lighting Techniques
Proper lighting is essential for enhancing defect visibility. Different lighting techniques offer advantages for various defect types:
- Coaxial illumination: Provides uniform lighting, minimizing shadows and enhancing the visibility of surface defects. Ideal for detecting scratches or cracks.
- Diffused illumination: Reduces glare and highlights subtle variations in surface texture. Useful for detecting particulate matter or delamination.
- Ring lighting: Provides even illumination around the vial, reducing shadows and improving the overall image quality. Effective for various defect types.
Consistent and uniform lighting optimization is critical for reliable defect detection sensitivity. The choice depends on the specific defects you're targeting.
Algorithm Calibration and Training
Accurate algorithm calibration and training are vital for minimizing false positives and false negatives. This typically involves:
- Machine learning techniques: Using machine learning algorithms allows the system to learn from a large dataset of representative samples, improving its ability to accurately identify defects.
- Data augmentation: Augmenting the training dataset with variations in lighting, vial orientation, and defect types helps improve the robustness of the algorithm.
- Regular algorithm updates: Regularly updating the algorithms with new data ensures that the system remains accurate and adaptable to changing conditions.
Effective algorithm calibration and model training using AI-powered inspection techniques are crucial for improving the accuracy of your image processing workflow.
Implementing Effective Quality Control Measures
Robust quality control measures are essential for ensuring the accuracy and reliability of the automated visual inspection process.
Establishing Clear Acceptance Criteria
Defining precise acceptance criteria is crucial:
- Regulatory compliance: Acceptance criteria must adhere to relevant regulatory guidelines (e.g., GMP).
- Internal quality standards: Establish internal standards to maintain consistent quality control beyond minimum regulatory requirements.
- Defect classification: Clearly classify different defect types (e.g., particulate matter, cracks, delamination) and define acceptable levels for each.
Clear acceptance criteria are vital for regulatory compliance and maintaining high quality control standards.
Regular System Maintenance and Validation
Regular maintenance and validation are crucial for maintaining accuracy and reliability:
- Preventive maintenance: A scheduled maintenance program minimizes downtime and ensures optimal system performance.
- Calibration procedures: Regular calibration ensures the accuracy of measurements and reduces the risk of errors.
- Validation testing: Regular validation testing verifies that the system meets its intended performance specifications.
Consistent system maintenance, including adherence to validation protocols, is necessary for maintaining system reliability.
Maximizing the Efficiency of Automated Visual Inspection
Optimizing automated visual inspection of lyophilized vials involves a multi-faceted approach. Selecting the right system, optimizing image acquisition and processing parameters, and implementing robust quality control measures are all crucial for maximizing efficiency, accuracy, and regulatory compliance. By carefully considering these strategies, pharmaceutical manufacturers can significantly improve product quality, reduce costs, and meet stringent regulatory requirements. Investing in and optimizing your automated visual inspection strategy is essential for the future of efficient and compliant lyophilized vial production.
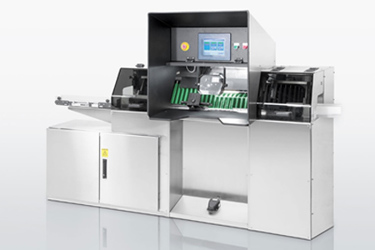
Featured Posts
-
The Impact Of Michael Kays Remarks On Juan Sotos Bat
May 12, 2025 -
Grand Slam Delight A Jamaica Observer Report
May 12, 2025 -
John Wick 5 Hope For An Ending But Doubts Remain
May 12, 2025 -
New Allegations Against Prince Andrew Undercover Video Surfaces
May 12, 2025 -
Knicks Vs Bulls Expert Betting Preview And Predictions For February 20 2025
May 12, 2025
Latest Posts
-
Unexpected Elimination In The Challenge Season 41 Spoilers Inside
May 12, 2025 -
Challenge Season 41 Spoiler Alert Unexpected Twist And Veteran Survival
May 12, 2025 -
Stream Over 100 Mtv Unplugged Performances Complete Episode Guide
May 12, 2025 -
Mtv Unplugged Full List Of 100 Episodes Available Now
May 12, 2025 -
Mtv Cancels 2025 Movie And Tv Awards Ceremony
May 12, 2025