F-35 Program Audit Exposes Critical Inventory Control Failures
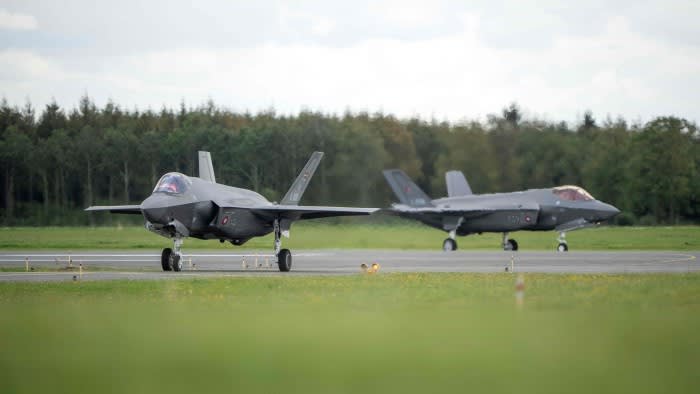
Table of Contents
The Audit's Key Findings: Uncovering the Extent of F-35 Inventory Control Failures
A comprehensive audit, involving the Department of Defense (DoD), the Government Accountability Office (GAO), and various contractors, revealed a systemic breakdown in F-35 spare parts management. The scope extended across the entire supply chain, impacting logistics and maintenance operations globally. The audit unearthed numerous instances of severe mismanagement, including:
- Lack of real-time inventory visibility: The audit found significant discrepancies between reported inventory levels and actual stock. This lack of accurate, up-to-the-minute data severely hampers effective planning and timely maintenance.
- Inefficient tracking of spare parts and components: Outdated tracking systems and a lack of standardized procedures led to significant difficulties in locating and managing critical F-35 spare parts. This resulted in prolonged search times and increased maintenance delays.
- High rates of missing or damaged parts: The audit documented a surprisingly high percentage of missing or damaged parts within the F-35 inventory. This points to failures in warehousing, handling, and quality control throughout the supply chain.
- Difficulties in predicting and fulfilling maintenance needs: The inability to accurately track parts and predict future requirements resulted in frequent delays in maintenance schedules, impacting the operational readiness of the F-35 fleet.
Root Causes of F-35 Inventory Control Problems: Identifying Systemic Weaknesses
The F-35 inventory control failures aren't isolated incidents; they stem from deeper systemic weaknesses within the program:
- Inadequate software and IT systems for inventory management: The audit highlighted the reliance on outdated and poorly integrated IT systems. A lack of a unified, real-time inventory management system significantly hindered effective tracking and control.
- Lack of integration between different supply chain stakeholders: The complex supply chain involves numerous government agencies, contractors, and international partners. Poor communication and data-sharing across these stakeholders created significant bottlenecks and inefficiencies.
- Insufficient training for personnel managing F-35 inventory: The audit suggested that personnel responsible for managing the complex inventory lacked the necessary training and expertise in modern supply chain management techniques.
- Poor communication and collaboration across government agencies and contractors: Silofication and a lack of effective collaboration hampered problem-solving and efficient inventory management.
Consequences of F-35 Inventory Control Failures: Impact on Operational Readiness and Costs
The consequences of these F-35 inventory control failures are far-reaching and severe:
- Increased aircraft downtime due to lack of spare parts: The shortage of critical parts leads to extended periods of aircraft downtime, directly impacting operational readiness rates.
- Delays in maintenance and repairs: The lack of readily available parts causes significant delays in maintenance and repair schedules, further impacting operational readiness.
- Reduced operational readiness of the F-35 fleet: The cumulative effect of these issues significantly reduces the overall operational readiness of the F-35 fleet, diminishing its effectiveness.
- Significant cost overruns associated with addressing the inventory issues: The costs associated with rectifying these problems, including procuring missing parts, upgrading IT systems, and improving training, will add significantly to the already substantial program costs, leading to further cost overruns.
Potential Solutions for Improving F-35 Inventory Control: Recommendations for Improvement
Addressing these critical F-35 inventory control failures requires a multi-pronged approach:
- Implementation of advanced inventory management software: Investing in modern, integrated inventory management systems capable of providing real-time visibility and predictive analytics is crucial.
- Improved data sharing and collaboration among stakeholders: Establishing clear communication channels and data-sharing protocols across all stakeholders is paramount to improving efficiency and accuracy.
- Investing in robust supply chain risk management: Proactive strategies for managing supply chain risks, including identifying potential disruptions and developing contingency plans, are essential.
- Development of standardized processes for inventory control: Implementing standardized procedures across the entire supply chain will improve consistency, accuracy, and efficiency.
Conclusion
The F-35 program audit clearly reveals the severity of the F-35 inventory control failures. These failures, stemming from systemic weaknesses in supply chain management, logistics, and IT infrastructure, have significant consequences for operational readiness and program costs. Addressing these issues requires immediate and decisive action, including investment in modern technology, improved training, and enhanced collaboration among all stakeholders. We must demand accountability and transparency in the F-35 program to prevent future F-35 inventory control failures and ensure the long-term success of this vital defense asset. For further information on this critical issue, refer to the latest GAO reports and DoD publications on the F-35 program.
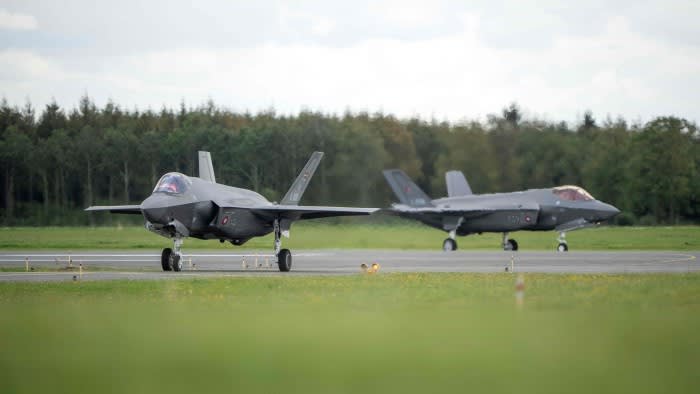
Featured Posts
-
Recordati Tariff Volatility Drives M And A Strategy In Italy
Apr 30, 2025 -
Dau Tu Gop Von Vao Cong Ty Nghi Van Lua Dao Cach Bao Ve Ban Than
Apr 30, 2025 -
Thunder Over Louisville Cancelled Impact Of Ohio River Flood On The Event
Apr 30, 2025 -
O Futuro Da Ia Meta Lanca App Para Competir Com O Chat Gpt
Apr 30, 2025 -
Is Age Just A Number Health Happiness And The Aging Process
Apr 30, 2025